The Importance of Maintaining Barrel Injection Molding Wear Tolerances
The Importance of Maintaining Barrel Injection Molding Wear Tolerances
Ensuring Precision in Injection Molding
The Role of Wear Tolerances
Injection molding is a manufacturing technique that demands careful attention to wear tolerances for components like screws and barrels. Reduced wear tolerances can improve manufacturing accuracy. To tight control over thickness deviations (e.g., ±0.05mm) ensures components meet exact specifications and reduce uneven wear and prolonging service life.
CHUANGRI SCREW focuses on crafting quality screw and barrel components with precision to meet strict wear tolerance standards.
CHUANGRI SCREW’s Commitment to Quality
At CHUANGRI SCREW ensuring wear tolerances isn’t just about accuracy, it’s about upholding top-notch product quality standards. The company utilizes state-of-the-art technologies and stringent quality control measures to guarantee that its injection molding screws and barrels do not meet but surpass industry benchmarks. By prioritizing customers and maintaining control over the production process they implement lean production management practices to ensure the efficacy of testing processes and consistently deliver exceptional product quality.
Enhancing Efficiency and Longevity
Benefits of Proper Maintenance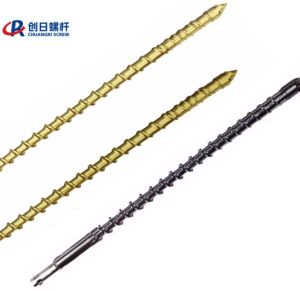
Maintaining injection molding equipment properly is key to improving efficiency and extending its lifespan effectively. CHUANGRI SCREW ensures that its products have wear tolerances to minimize maintenance needs and lower downtime and costs for manufacturers. Their emphasis on durability and performance allows clients to depend on their equipment for periods without sacrificing efficiency.
CHUANGRI SCREW’s Advanced Technologies
CHUANGRI SCREW uses technologies in its manufacturing methods to create screws and barrels that are extremely resistant to wear and tear. For example, the Coated Injection Molding Screw has a coat of chromium metal on the metal surface. The chrome plating layer is generally between 10 microns and 50 microns in thickness and has enhanced adhesion and wear resistance. It is particularly well suited to screws used in high-temperature and highly corrosive applications. This innovative approach not only increases the lifespan of their products but also maintains the same level of performance even in unfavorable conditions.
Optimizing Production with High-Quality Components
Importance of Screw Injection Molding
Screw injection molding plays a role in manufacturing by demanding precision and quality to guarantee top-notch performance levels. The screw melts and mixes plastic particles uniformly, ensuring consistent flow into the mold cavity. This prevents defects like voids or warping, aligning with the emphasis on precision and dimensional accuracy in mold design. The automated screw-driven systems enable rapid cycles and high-volume output (e.g., mass-producing automotive components or appliance casings), it is crucial for cost-effective large-scale production.
CHUANGRI SCREW screws are crafted to work with a range of plastic materials by incorporating specific features like a screw diameter that varies from Φ14mm to Φ250mm while focusing keenly on maintaining exact tolerances. Their components are built for performance in various usage scenarios. These efforts towards excellence not only boost the effectiveness of injection molding but also extend the lifespan of the machinery.
Barrel Injection Molding Excellence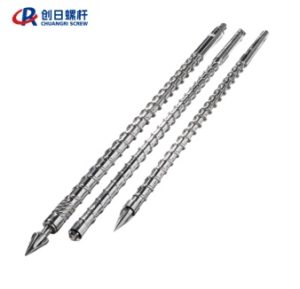
CHUANGRI SCREW’s dedication to producing top-quality barrels guarantees that their products perform reliably in challenging situations. CHUANGRI SCREW combines the simplicity and cost-effectiveness of traditional three-zone screws with the productivity and quality advantages of optimized material feeding, melting and metering zones. It is considered the best choice for injection molding applications. The technology processing of Solid Carbide Screw is the solid carbide with the dimensions of 10 mm to 300mm. It is used for household items, electronic products, automotive parts and so on. It is also capable of processing materials containing up to 75% glass fiber.
Frequently Asked Questions
Q: What measures does CHUANGRI SCREW take to ensure wear resistance?
A: CHUANGRI SCREW utilizes advanced methods to improve the durability of their products with a special focus on bimetals barrels where they apply a 2 to 5-mm thick alloy coating on the inner wall of the barrel for exceptional resistance against corrosion and abrasion, with the ability to withstand high temperatures during operation resulting in a significantly prolonged lifespan compared to conventional nitrided alternatives. Furthermore, CHUANGRI SCREW uses alloy powders that are sprayed and welded onto the screw flights to cater to various purposes. This process enhances the durability and efficiency of their components significantly.
Q: How does CHUANGRI SCREW guarantee the quality of their injection molding screws and barrels?
A: The R&D department of CHUANGRI SCREW is manned by a group of highly qualified and creative professionals comprising specialists with abundant experience in the industry as well as professors and chief engineers who employ advanced design software, such as Auto CAD and Solid Works to continuously innovate product design and produce better quality products while designing new ones to satisfy your requirements efficiently.
Q: How does maintaining wear tolerances impact production costs?
A: Keeping the wear tolerances accurate plays a role in cutting down production expenses significantly for CHUANGRI SCREW products by making sure each part functions at its best efficiency level. It will reduced downtime and maintenance costs. Secondly, by using cost-effective MRO parts with controlled wear tolerances, companies could reduce overstocking of replacements and avoid shortages, this will balancing inventory costs while ensuring operational continuity. Properly maintained tolerances ensure machinery operates at peak performance, supporting the goal of simplified manufacturing processes and higher output quality. This feature reduces rework costs, and improves production efficiency.